The spindle system is a key component of the machine to generate vibration. Analyzing the dynamic characteristics of the spindle can understand the vibration resistance and deformation modes of the machine tool. In the analysis, the main shaft and the support bearing are simplified into an elastic system, and the centrifugal force generated by the rotation of the main shaft is taken as the prestress of the structure. This method provides a new idea for the dynamic analysis of the main shaft components.
Introduction <br> <br> paper, CNC vertical spindle automatic loading and unloading systems for the study, research affect the stability and anti-vibration capability of the spindle shaft design system. The main shaft and the support bearing are simplified into a flexible system, and the centrifugal force generated by the rotation of the main shaft is used as a prestressed force for analysis, which provides a new analytical idea for the analysis of the main shaft components.
The finite element method is widely used in the analysis and calculation of mechanical engineering. In this paper, finite element analysis of the spindle of the machine tool firstly requires the establishment of a finite element model of the spindle, which includes setting material parameters, dividing the grid, and applying boundary conditions to the spindle model. The boundary conditions can take into account the bearing support factors, ie adding elastic constraints with stiffness values ​​at the bearing support locations. Using the finite element method, we can perform modal analysis and harmonic response analysis on the main shaft.
1, modal analysis <br> <br> spindle when the spindle is rotated, the center of mass offset from the axis of the shaft will generate a periodically varying direction of the inertial force, the inertia force is the main axis of the lateral vibration stirred. When the spindle speed approaches or passes its own critical speed, its vibration will appear abnormally strong. Modal analysis can determine the natural frequency and vibration mode of the mechanism, so as to avoid excessive vibration when the spindle works.
1.1 The theoretical basis of modal analysis The finite element theory gives the dynamic equation of the main shaft as follows:
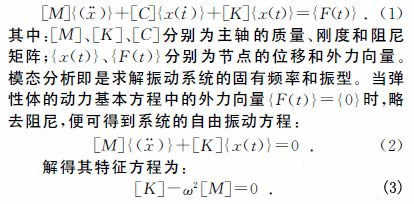
Where: ω is the natural frequency of the system 1.2 Spindle Structure Design As the object of analysis and analysis, the spindle has selected two kinds of design structures. One is the long axis structure (see Figure 1) and the other is the short axis structure (see Figure 2). As can be seen from Figure 1, the major axis of the design of the spindle is an elongated shaft length of 736mm. On the other hand, the length of the central axis of the hollow shaft of the second design is significantly reduced to 280 mm and the diameter is relatively increased. It can be seen that the shape and size of the spindle structure in these two schemes are all different, and the modal parameters of the structure can be calculated by finite element analysis, and the comparison result can determine which structure is better.
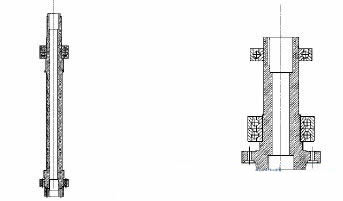
Fig.1 Structure of long axisFig.2 Structure of short axis 1.3 Modal analysis boundary conditions According to the actual situation, the spindle works under the restrictions of other components, which is to set the corresponding constraints. As a component that supports the main shaft, the bearing stiffness plays a decisive role in the accuracy and vibration resistance of the rotor system. The support of the bearing to the spindle can be simulated as an elastic constraint imposed on the fitting portion of the spindle and the bearing (as shown in Fig. 3). At the same time, the locking nut and other structures at the upper end of the spindle limit the X, Y and Z degrees of freedom of the spindle.
There are several methods to identify bearing support parameters, such as transfer function method, direct method, etc. This paper uses existing empirical formulas to calculate the stiffness of angular contact bearings. The spindle bearing adopts the positioning pre-tightening method. Under the known pre-tightening force, the radial stiffness Kr of the angular contact ball bearing can be approximated:
Figure 3 equivalent spring position diagram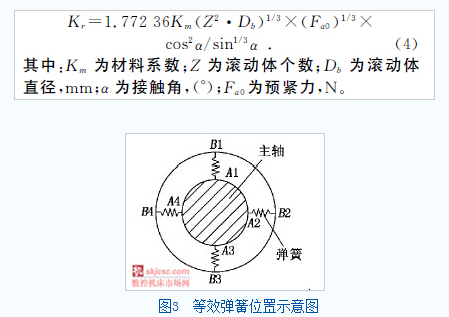
1.4 Results of modal analysis with prestress According to the known parameters, the finite element preprocessing of the spindle is set, and the elastic constraint is imposed according to the constraint conditions. In order to consider the influence of the centrifugal stress when the rotor rotates, it is necessary to set a rotation speed for the spindle, that is, the structural modal analysis with prestress. The results of the first three modal modes of the two structural principal axes are shown in Tables 1 and 2 .
Table 1 The natural frequency and mode shape of the hollow minor axis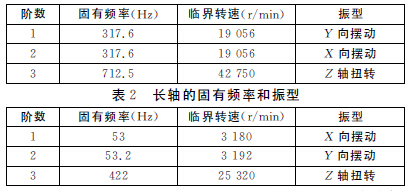
From Table 1 and Table 2, it can be seen that the critical speed of the long axis is much smaller than the critical speed of the short hollow shaft. The rotation speed during processing is 3000r/min, the idle speed is 3500r/min, and the low-order critical speed of the long axis is 3180r/min and 3192r/min. It can be seen that large vibrations may occur during the processing of the long axis. The critical speed of the short axis is much greater than the actual speed, avoiding the possibility of resonance.
2, the spindle <br> <br> harmonic analysis harmonic analysis is to study changes in strain and stress generated in the object by an excitation force within a certain frequency range, the main constraint study by modal analysis with the same, is applied The load is 60 N·m of torque. Displacement data acquisition was performed with the leading end of the long axis and the short axis respectively. The sampling interval was 4 Hz, and 20 sampling points were uniformly obtained in the test range of the torque load of 0 Hz to 80 Hz. The calculation data at the sampling frequency is connected to the curves shown in FIG. 4 and FIG. 5 , and the deformation of the main shaft under the load in this frequency range can be analyzed.
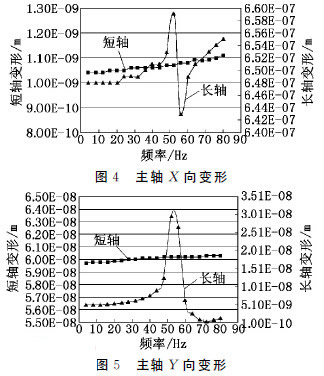
3 Conclusion <br> <br> contemplated herein supporting bearing stiffness modal analysis, the centrifugal stress and the spindle rotation as prestressing, the design of the spindle Solving for low order natural frequencies and mode shapes. The comparison shows that the short axis of the hollow has better dynamic characteristics than the long axis. In this paper, the harmonic response analysis is also performed. The results show that under the sinusoidal force with a certain frequency change, the deformation of the hollow short-axis structure is smaller, which is also consistent with the results of modal analysis.
Introduction <br> <br> paper, CNC vertical spindle automatic loading and unloading systems for the study, research affect the stability and anti-vibration capability of the spindle shaft design system. The main shaft and the support bearing are simplified into a flexible system, and the centrifugal force generated by the rotation of the main shaft is used as a prestressed force for analysis, which provides a new analytical idea for the analysis of the main shaft components.
The finite element method is widely used in the analysis and calculation of mechanical engineering. In this paper, finite element analysis of the spindle of the machine tool firstly requires the establishment of a finite element model of the spindle, which includes setting material parameters, dividing the grid, and applying boundary conditions to the spindle model. The boundary conditions can take into account the bearing support factors, ie adding elastic constraints with stiffness values ​​at the bearing support locations. Using the finite element method, we can perform modal analysis and harmonic response analysis on the main shaft.
1, modal analysis <br> <br> spindle when the spindle is rotated, the center of mass offset from the axis of the shaft will generate a periodically varying direction of the inertial force, the inertia force is the main axis of the lateral vibration stirred. When the spindle speed approaches or passes its own critical speed, its vibration will appear abnormally strong. Modal analysis can determine the natural frequency and vibration mode of the mechanism, so as to avoid excessive vibration when the spindle works.
1.1 The theoretical basis of modal analysis The finite element theory gives the dynamic equation of the main shaft as follows:
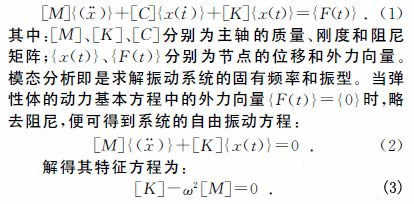
Where: ω is the natural frequency of the system
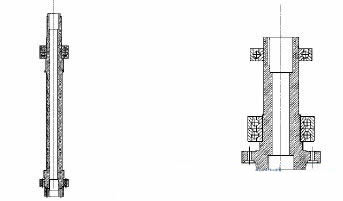
Fig.1 Structure of long axisFig.2 Structure of short axis
There are several methods to identify bearing support parameters, such as transfer function method, direct method, etc. This paper uses existing empirical formulas to calculate the stiffness of angular contact bearings. The spindle bearing adopts the positioning pre-tightening method. Under the known pre-tightening force, the radial stiffness Kr of the angular contact ball bearing can be approximated:
Figure 3 equivalent spring position diagram
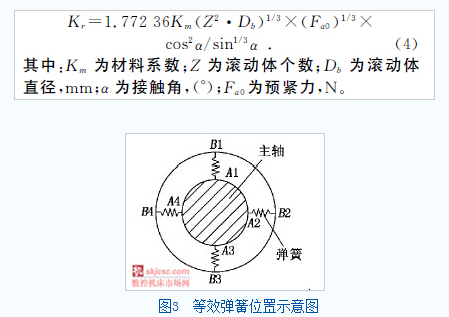
1.4 Results of modal analysis with prestress
Table 1 The natural frequency and mode shape of the hollow minor axis
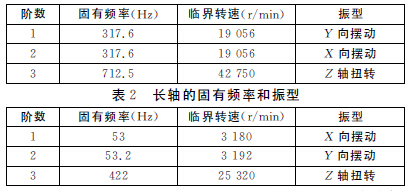
2, the spindle <br> <br> harmonic analysis harmonic analysis is to study changes in strain and stress generated in the object by an excitation force within a certain frequency range, the main constraint study by modal analysis with the same, is applied The load is 60 N·m of torque. Displacement data acquisition was performed with the leading end of the long axis and the short axis respectively. The sampling interval was 4 Hz, and 20 sampling points were uniformly obtained in the test range of the torque load of 0 Hz to 80 Hz. The calculation data at the sampling frequency is connected to the curves shown in FIG. 4 and FIG. 5 , and the deformation of the main shaft under the load in this frequency range can be analyzed.
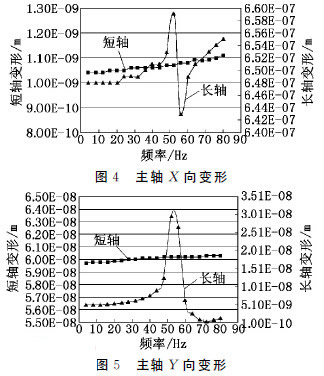
Fiberglass Filter Bag has the unique gap of ordinary felt filter cloth, good air permeability, high efficiency dust collecting and long service life. Its temperature resistance grade is moderate, instantly up to 150 degrees , acid and alkali resistance is moderate, and has very good wear resistance.
Fiberglass Filter Bag
Fiberglass Filter Bag,Dust Collector Bags,Fiberglass Non-Woven Filter Bag,Fiberglass Dust Collector Filter Bag
Hebei Wangjing Environmental Protection Co., Ltd. , https://www.wjdustcollector.com