EFI module test system is composed of NI tester, analog load box, power supply, barcode scanning and test fixture. After the tester manually puts the module into the fixture and scans the bar code, the system will automatically execute the module power consumption, input resistance to ground, A/D sampling value, output leakage current, FET clamp voltage, E2PROM checksum, etc. Item test. At the same time, the test data and pass/fail status are recorded, and the data is automatically stored as a TXT file for future data analysis.
First, hardware structure EFI test system hardware structure see Fig. 1.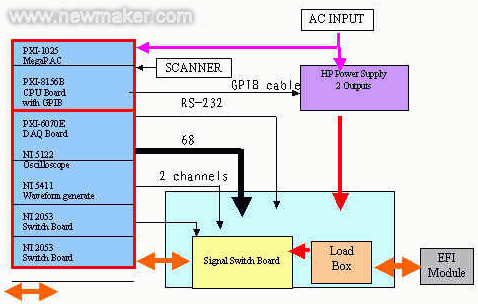
It includes NI testers (CPU, DAQ, OSC, WAVEFORM GENERATE, MATRIX SWITCH), analog load boxes, power supplies, bar code scanning, and test fixtures.
The detection of the module includes three parts: input port hardware, output port hardware, and function detection under specific operating conditions. In order to complete the input port hardware detection, PXI-6070E multi-function card is used for data acquisition. It has 64 channels of 12-bit analog input, 2 analog outputs, and 8 digital I/O ports. The port switch uses the NI-2503 switch card, which is a two-wire 24-bit switch card that is responsible for connecting the port under test to the acquisition card PXI-6070E.
Similarly, hardware switching to the output is done by another NI-2503 card. Data acquisition was done using an NI-5112 oscilloscope card. Its 100MHz bandwidth ensures the acquisition of ignition and injection pulses. The collected data will be placed in the specified buffer. Through data analysis, we can get the maximum value and frequency of the output signal pulse.
After the detection of the hardware is completed, the BOOTSTRAP mode is also used to send the calibration data to the module E2PROM, and then the chip is switched to the monolithic mode. Simulate the working status of the normal operating condition detection module and complete the function test under specific working conditions. Through the above tests, the reliability of the module is ensured.
Second, the software design In the environment with a computer and the corresponding hardware card, LABWINDOWS with its C-based development environment, a good user interface (as shown in Figure 2), powerful library functions and convenient and fast debugging means that the design Can design, debug and develop the actual test system with the fastest speed, greatly reducing the workload.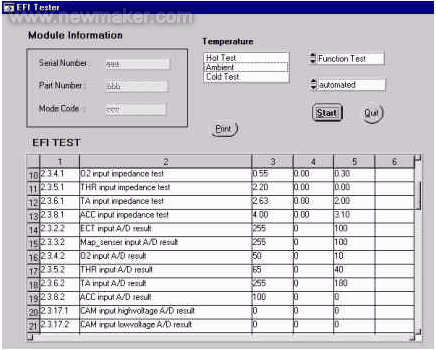
Module detection system software can work in three modes:
A. Hardware Diagnostic Mode B. Functional Test Mode C. EOL Test Mode Hardware detection of the input port can be easily accomplished by calling the NI-2503, NI-5112, and PXI-6070E drive functions.
A/D sampling value of the chip and hardware detection of the output port need to download a special test program (about 1 KB in assembly language). The use of software programming, we must first enter the 68HC11 BOOTSTRAP mode, and then download the dedicated test program to the chip. By calling a subroutine of a dedicated test program, it can be completed including read/write chip RAM, E2PROM area, check RAM, E2PORM area, A/D sampling value reading, setting PWM output pulse, checking version number and many other functions .
Functional test, the chip works in monolithic mode, by calling the NI-5411 arbitrary waveform generator driver function to simulate the 60-2 waveform of the speed signal, and input the corresponding voltage signal to simulate the sensor signal input, complete the specific Functional tests under operating conditions.
All test results will be stored in the specified file for statistical CPK and data analysis.
Third, analysis and evaluation Through the above practical application, the test system developed by LABWINDOWS software has the following significant advantages:
1. Accelerate the development cycle of the system and reduce the development difficulty. The use of LABWINDOWS can easily call hardware drivers and function functions, reducing the work intensity and speeding up the development process.
2. Reduced test cycles. Using LABWINDOWS, the data transmission speed and measurement time are improved, the product measurement time is reduced, and the measurement time of each module is less than 50 seconds.
3. Has a high degree of versatility. Using the same hardware environment, only fine-tune the software to measure ECS, DIS and other products.
First, hardware structure EFI test system hardware structure see Fig. 1.
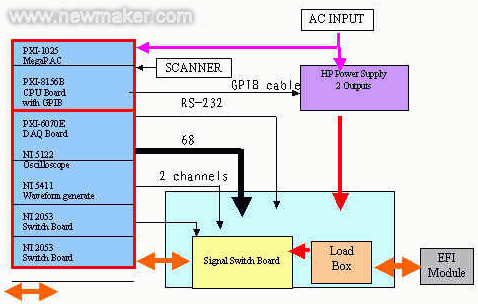
Figure 1 EFI test system hardware structure
It includes NI testers (CPU, DAQ, OSC, WAVEFORM GENERATE, MATRIX SWITCH), analog load boxes, power supplies, bar code scanning, and test fixtures.
The detection of the module includes three parts: input port hardware, output port hardware, and function detection under specific operating conditions. In order to complete the input port hardware detection, PXI-6070E multi-function card is used for data acquisition. It has 64 channels of 12-bit analog input, 2 analog outputs, and 8 digital I/O ports. The port switch uses the NI-2503 switch card, which is a two-wire 24-bit switch card that is responsible for connecting the port under test to the acquisition card PXI-6070E.
Similarly, hardware switching to the output is done by another NI-2503 card. Data acquisition was done using an NI-5112 oscilloscope card. Its 100MHz bandwidth ensures the acquisition of ignition and injection pulses. The collected data will be placed in the specified buffer. Through data analysis, we can get the maximum value and frequency of the output signal pulse.
After the detection of the hardware is completed, the BOOTSTRAP mode is also used to send the calibration data to the module E2PROM, and then the chip is switched to the monolithic mode. Simulate the working status of the normal operating condition detection module and complete the function test under specific working conditions. Through the above tests, the reliability of the module is ensured.
Second, the software design In the environment with a computer and the corresponding hardware card, LABWINDOWS with its C-based development environment, a good user interface (as shown in Figure 2), powerful library functions and convenient and fast debugging means that the design Can design, debug and develop the actual test system with the fastest speed, greatly reducing the workload.
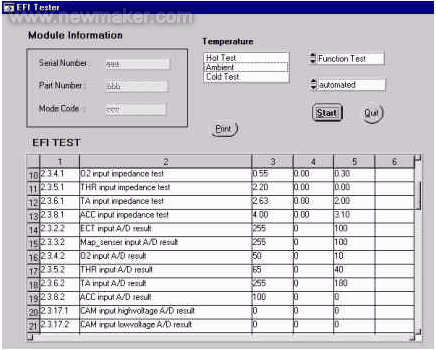
Figure 2 LABWINDOWS good user interface
Module detection system software can work in three modes:
A. Hardware Diagnostic Mode B. Functional Test Mode C. EOL Test Mode Hardware detection of the input port can be easily accomplished by calling the NI-2503, NI-5112, and PXI-6070E drive functions.
A/D sampling value of the chip and hardware detection of the output port need to download a special test program (about 1 KB in assembly language). The use of software programming, we must first enter the 68HC11 BOOTSTRAP mode, and then download the dedicated test program to the chip. By calling a subroutine of a dedicated test program, it can be completed including read/write chip RAM, E2PROM area, check RAM, E2PORM area, A/D sampling value reading, setting PWM output pulse, checking version number and many other functions .
Functional test, the chip works in monolithic mode, by calling the NI-5411 arbitrary waveform generator driver function to simulate the 60-2 waveform of the speed signal, and input the corresponding voltage signal to simulate the sensor signal input, complete the specific Functional tests under operating conditions.
All test results will be stored in the specified file for statistical CPK and data analysis.
Third, analysis and evaluation Through the above practical application, the test system developed by LABWINDOWS software has the following significant advantages:
1. Accelerate the development cycle of the system and reduce the development difficulty. The use of LABWINDOWS can easily call hardware drivers and function functions, reducing the work intensity and speeding up the development process.
2. Reduced test cycles. Using LABWINDOWS, the data transmission speed and measurement time are improved, the product measurement time is reduced, and the measurement time of each module is less than 50 seconds.
3. Has a high degree of versatility. Using the same hardware environment, only fine-tune the software to measure ECS, DIS and other products.
Carbon Steel Pipe,Carbon Seamless Steel Pipe,Astm A135 Seamless Carbon Steel Pipe,6M Carbon Seamless Steel Pipe
Liaocheng Changyi Metal Material Co.,Ltd , https://www.changyisteel.com