1 Introduction
The company under the China Nonferrous Metal Industry Corporation. Concentrate manufacturers, China's largest molybdenum. The mine is located in Huaxian County, Shaanxi Province, and the deposit was discovered in the 1950s. At the end of 1962, the first plant was put into operation. In September 1971, the second plant was put into operation, and it was expanded in 1981. In September 1984, the third plant was put into operation, with a production capacity of more than 20kt.
Up to now, the mining capacity has reached more than 20kt per day. It also has a 9kt/a molybdenum concentrate roasting capacity.
2. Deposits, ores and mining
Deposit is - the high-temperature hydrothermal stockwork porphyry molybdenum deposit, molybdenite is the most important and valuable minerals, has a comprehensive recovery value are pyrite, yellow copper ore, magnetite. The middle part of the mining area is granite porphyry, and both sides are Anshan porphyrite. The ore body is found in the granite porphyry and the Anshan shale rock in contact with it.
The ore body is a giant lenticular body with a long axis of 30° from north to south and a length of about 2200 m. The east-west direction is a short axis and the width is about 600-800 m. The vertical is very steep and nearly upright, and the vertical depth is 600~700m. The ore body is huge, the shape is simple, and the mineral occurrence and grade change are relatively stable. The middle part of the ore body has higher molybdenum and gradually becomes poorer in the north-west, south-east and deep. There is usually no obvious boundary between the ore body and the surrounding rock, which is a gradual change. The width of the transition zone is about 150m, and only the north-west direction is cut by the Yanmen concave fault. The upper plate of the fault is the ore body, and the lower plate is the surrounding rock with clear boundary.
The ore body is a product of multi-stage gas-water hydrothermal activity, with high, medium and low temperature mineralization. However, the early or late rock mass is basically free of molybdenum, and the molybdenite is in the high-medium temperature hydrothermal section. It is mainly produced in the hexagonal 2H type. Separable ore mineralization following stages: (1) Quartz - feldspar vein phase, minerals are: orthoclase, plagioclase, quartz, white mica, calcite and molybdenite, pyrite, magnetic iron ore. This vein is often cut through other veins. (2) Quartz-molybdenum veins, the early molybdenite in this type of vein is more than later. There are more in the center of the ore body than in the side. Molybdenite minerals in the pulse-like shape consisting of a blade assembly scattered manner, in the film-like walls of veins, vein quartz and banded in parallel. Symbiotic minerals include magnetite, fluorite and a small amount of cassiterite and muscovite. (3) Sulfide and quartz stage: sulfide containing copper, lead , iron, etc. Contains no or less molybdenum ore. (4) Non-metallic minerals (non-mineral colloids) - quartz veins. These colloids are mostly filled in the fracture zone and never have molybdenite.
Ore: An ore body composed of the above veins interlaced to form a network. The average grade of molybdenum in the ore is 0.098%, the other 0.023% Cu, 2.27% S (FeS 2 ), 0.05% to 0.01% Pb. The ore density is 2.7g/cm 3 and the Platts hardness is 12~14.
There are three types of ore: Anshan porphyry (more than 70%); granite porphyry (more than 20%) distributed in the middle of the ore body throughout the ore body; quartzite and slate slate (about 3%).
The main metal mineral in the ore is sulfide, while the oxide only accounts for 1.5% of the total metal mineral reserves. The main metallic minerals: molybdenite, pyrite, followed magnetite, chalcopyrite, and galena, sphalerite, cassiterite bismuthinite and the like. The main gangue is quartz and feldspar, followed by fluorite, muscovite, biotite, sericite and calcite.
The molybdenite structure is mainly 2H type, and the 2H+3R type is rare. The latter is mainly distributed at the edge of the ore body, especially in the fracture zone. The morphological and scaly aggregates are in the form of fine veins, thin films and scattered spots in the gangue and near-vein surrounding rocks, mostly concentrated in the quartz veins. The particle size is generally 0.027~0. 05mm. According to the fluid inclusion uniform method, the molybdenum ore-forming temperature is between 434 and 234 °C, and mainly between 400 and 260 °C. The burst method is 365~580 °C, generally above 400 °C, which is a product of medium-high temperature hydrothermal fluid. The pressure side of the mineral inclusions is set at 26 to 40 MPa, and most of them are about 34 MPa. The thickness of the overlying stratum is about 1~2km. [next]
Pyrite is self-formed and uniformly distributed in the gangue. The particle size is coarse, with a maximum of 2 mm and a minimum of 0.03 mm, generally 0.045 mm. According to Zhou Guohua et al., S/Fe=1.98~2.01. Easy to choose easy to suppress.
The chalcopyrite has a particle size of 0.01 to 0.1 mm, generally 0.04 mm, and is symbiotic with pyrite, magnetite, and molybdenite.
The deposit is one of the six major molybdenum mines in the world and is a giant main molybdenum deposit. The ore in the table, the average grade of molybdenum is 0.100%, and the average grade of ore and molybdenum is 0.038%. In addition, there are oxidized ores with an average of 0.099% molybdenum and a molybdenum metal reserve of more than 100 kt.
The deposit is also accompanied by copper, grade 0.028% Cu; pyrite, grade 2.813% FeS 3 ; niobium , grade (in molybdenum concentrate) 0.0017% Re.
The ore body is huge, and the north-west end is exposed to the surface, only partially covered with 0~15m Quaternary sediments, which is suitable for large-scale open-pit mining. Now, the open pit has entered the peak of production.
Due to large-scale mining, production statistics in March 1988, the ore loss rate in open pit mining is only 0.069%, the ore depletion rate is only 0.07%, and the rock mining and stripping ratio is extremely low.
3. Introduction to a selection plant
The process flow is shown in Figure 1.
Figure 1 Jinduicheng First Plant Process
Broken: Two sections open and broken. One set of 400×600mm jaw crusher and one set of ¢900mm medium cone crusher . The final crush size is 93%-25mm.
Rough grinding, rough selection: divided into two series. Each series consists of 1 set of 2.4×2.lm ball mill and 1 set of ¢1.5m high-single single spiral classifier. The grinding machine capacity is 8t/h·table, and the overflow level of the overflow is 60%~65%-200 mesh. The grading overflow flows through a rough two sweeping three fine flotation process. The crude concentrate grade is 5%~7% Mo, and the crude recovery rate is 85%~88%. It is selected after the ¢6m thickener is used for deodorization, and the tailings are discarded (for comprehensive recovery of pyrite). The sweep uses the 4A flotation machine 20 tanks, and the I~II times selects the 3A flotation machine 14 tanks. [next]
Re-grinding-selection section: The coarse concentrate is concentrated and decontaminated by the thickener, and then concentrated into the selected section, which runs 5~7h daily. It adopts two-stage re-grinding and eight selections of one-time fine sweeping selection process.
One section was reground with a ¢5×3.0m lattice type ball mill, and two é—250mm swirling machines were closed. The overflow fineness is 85%-200 mesh. Overflow through the 3A flotation machine 18 sets of IV to VI three selection of a fine sweep selection, fine sweep tail waste, VI fine bubble into the second-stage re-grinding system.
The second-stage re-grinding consists of two closed circuits of a 900×1800mm ball mill and a ¢125mm cyclone. The overflow fineness is 85%-400 mesh. The overflow is then selected by the VII~VIII times of the 20A flotation machine. The fine tail returns to the first stage and is reground, and the fine bubble is filtered. The concentrate grade is ≥53.5% Mo, and the molybdenum recovery rate of the selected section is 97%~97.5%.
Filtration and dry operation; VIII fine bubbles were dried by lm 2 round external filter, dried and dried to obtain the final molybdenum concentrate.
Agents: kerosene (collector), consumption 180 ~ 250g / t; 2 # oil (foaming agent) 100 ~ 150g / t; sodium cyanide (inhibition copper) 40 ~ 66g / t; waterglass 100 ~ 500g /t.
Concentrate quality: grade: 53.5% Mo, 0.15% Cu , 0.1% CaO, won the 1983 National Quality Silver Quality Award.
4, Jinduicheng Second Selection Plant
Process and equipment are shown in Figure 2.
Figure 2 Jinduicheng Second Plant Breaking Process
Broken: The original design was broken in three stages, and the final particle size was -25mm. In 1981, it was changed to three-stage closed-circuit crushing, and the final particle size was -15mm.
Rough selection section: One rough and one sweep selection, the process and equipment are shown in Figure 3, totaling four series. Each series consists of a ¢3.6×4.0m ball mill and a ¢3m double helix to form a closed-circuit grinding; the CHF-X14 inflatable flotation machine 10 tanks, 6A flotation machine 6 tanks constitute a rough selection, one sweep and one coarse Selected process flow.
Figure 3 Rough grinding rough selection process of Jinduicheng Second Selection Plant
[next]
Ball mill ball load: 69~75t/set, initial steel ball ¢120mm 50%, ¢l00mm25%, ¢80mm 15%, ¢60mm 10%. Only one kind of steel ball of 120mm is added in the production. The ball filling rate of the ball mill is 43%~44%, and the steel ball consumption is 1.5~1.6kg/t. The grinding concentration is 70.0%~79%, the grinding machine capacity is 70~73t/h·table, and the graded overflow fineness is 60~65%-200 mesh.
The coarse selection section gives the ore grade 0.09%~0.11% Mo, the coarse concentrate grade 2%~3%Mo, and the tailings grade 0.016%~0.023%. The molybdenum recovery rate is about 85%, and the tailings recover pyrite.
Re-grinding the selected section: the second section is re-grinded 9 times and 1 time is selected. The process is shown in Figure 4. A section of re-grinding uses 2 sets of ×1.5×3.0m ball mills, and the cyclone overflow fineness is 85%-200 mesh. The selected 3 concentrates are then re-grinded into the second stage, and the cyclone overflow fineness is 50%-400 mesh. After the second stage of re-grinding, the final product was obtained through six selections.
Figure 4 Jinlucheng Second Selection Plant Molybdenum Selection Process
Filtration: The final selected foam is concentrated by a 30m thickener to make the concentration reach 30% or more, and then filtered through a l0m 2 cylinder vacuum filter, and the filter cake is sent to the drying kiln. The mineral processing and pharmaceutical systems are shown in Table 1.
Table 1 Jinduicheng Second Selection Plant (produced in 1987) Pharmacy System
Drug | Dosage (g/t) | Add location |
Kerosene | 201 | Ball mill, rough sweep, II fine, V fine |
2 #æ²¹ | 104 | Stirring tank, coarse sweeping, sulfur rough selection, sulfur sweeping |
Sodium cyanide | 72 | VI fine, VII fine, IX fine |
Yellow medicine | 57 | Sulfur rough selection, sulfur sweeping |
Mineral processing indicators (production statistics for the whole year of 1987):
The ore grade is 0.117% Mo, the fineness of grinding is 58.78%-200 mesh, and the ore processing capacity is 1500 kt/a. The concentrate grade is 45.68% Mo, the impurity content is 0.162% Cu, 1.345% CaO, 11.80% SiO 2 ; the molybdenum recovery rate is 80.81%; the concentrate production is 3153t. [next]
5. Jinduicheng Third Selection Plant
Scale: 15 kt / d. Broken: three sections and one closed circuit. Rough selection: one rough selection, two selections, and two sweeps, as shown in Figure 5. There are nine parallel systems. Each system consists of a 3.6×4.0m lattice ball mill and a m3.0m high-twist double-helix classifier to form a closed-circuit grinding. Rough selection, sweep selection of 7A flotation machine, selected 6A flotation machine.
Featured section: divided into 3 series. The three series of coarsely selected concentrates merged into a selection of series. The design process is two-stage re-grinding, 9 times (fine 3~11), and the process is shown in Figure 6. The production process is a re-grinding, 9 selections (fine 3~11). Re-grinding uses a ¢2.1×3.6m overflow ball mill and 4 ¢300mm cyclone closed circuits. The selection uses a 4A flotation machine. Fine 3~11, each series shares 24 slots of 4A flotation machine, and the number of slots is 4, 4, 4, 4, 2, 2, 2, 1, and 1.
Figure 5 Rough grinding rough selection process of Jinduicheng Third Selection Plant
Figure 6 Jinduicheng Third Selection Plant Selection Process
[next]
Production indicators: 1987 statistics are listed in Table 2 and Table 3.
Table 2 Production Indicators of Jinduicheng Third Selection Plant
Project | Raw ore | Molybdenum concentrate | Molybdenum concentrate contains impurities (%) |
Processing capacity (kt/a) | grade(%) | Grinding fineness (%-200 mesh) | Production (t/a) | grade(%) | Yield (%) | Cu | CaO | SiO 2 |
Design | 4950 | 0.1 | 65 | 9350 | 45.00 | 85 | | | |
Produced in 1987 | 3146 | 0.118 | 62.76 | 6488 | 46.87 | 80.66 | 0.162 | 1.25 | 10.59 |
Table 3 Jinduicheng Third Selection Plant Pharmacy System
Drug | Design consumption (g/t) | Production consumption in 1987 (g/t) | Dosing point |
Kerosene | 360 | 225 | Ball mill feeding, rough sweep 1, 2, selected mixing tank, fine sweep 1, 2 |
2 #æ²¹ | 140 | 106 | Rough selection of agitation tank, coarse sweep 1, 2, sulfur coarse selection agitation tank, sulfur sweep |
Cyanide agent | 100 | 85 | Selected mixing tank, fine 1, 4, 8, 9, 10 |
Yellow medicine | 30 | 67 | Sulfur mixing tank, sulfur sweeping |
Phospho- x | | | Selected mixing tank, fine sweep 2, 5 fine |
Jinduicheng Molybdenum Industry Co., Ltd. is the largest molybdenum production base in China. Although its ore grade is low and the molybdenum ore is finely divided, the production index and production management are still relatively advanced in China.
Product information:
Inner layer: PTFE
Enhancement layer:stainless steel wire braid ( AISI Steel 304 316 )
Outer layer: PVC, PU(black, red, blue, yellow, purple, clear, gray, orange, ect.)
Temperature range: −65℃ ~ +260℃
Product performance: high temperature resistance,low temperature resistance,long lasting and good durability,acid and alkali resistance,ozone resistance,low coefficient,anti-friction, long using life and non-aging.
Purpose: widely used in Automotive, Bicycle, Motorcycle, Racing, Brake Lines, Clutch Lines, Fuel Systems, Turbo oil feed Hose, Coolant Systems, Oil Pressure Systems, Gauge lines & Power Steering.
Compatibility: Brake Fluids, Unleaded Petrol, Methanol, Water, & Oil. Ideal for use with Unleaded fuel, ect.
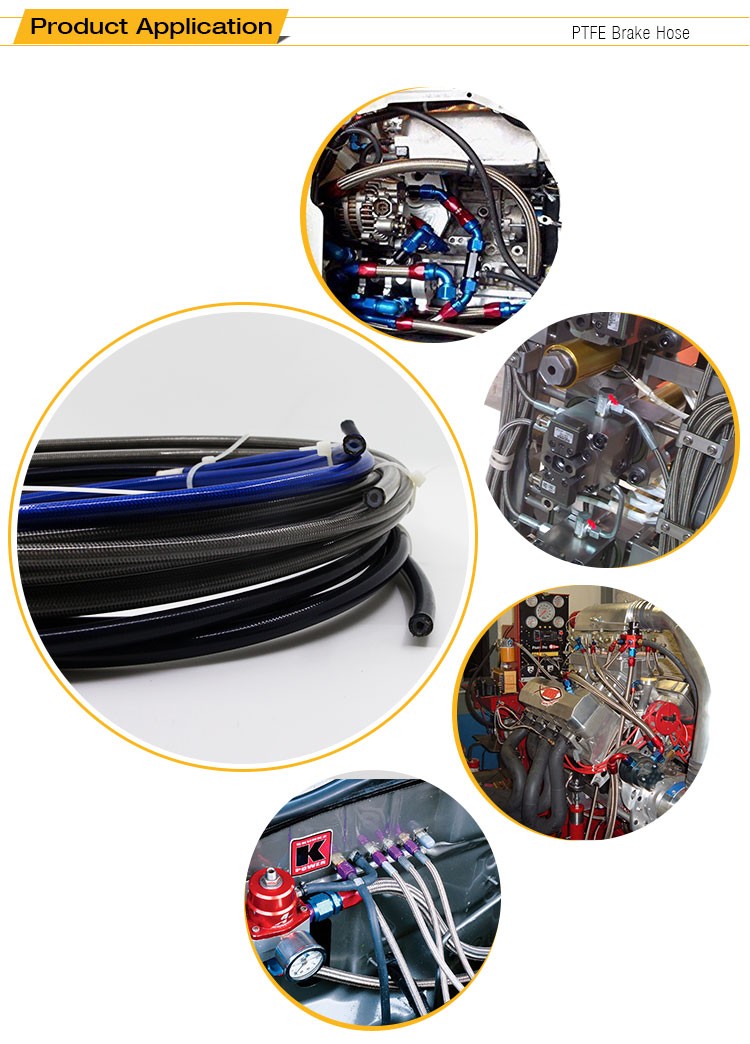
Air Hose
Air Hose,Pvc Air Hose,Flexible Air Hose,Rubber Air Hose
Hangzhou Hanray Industry Co., Ltd , https://www.airsuspensionride.com